Predictive Maintenance
Predictive Maintenance is a proactive maintenance strategy that uses data analysis tools and techniques to detect anomalies in operation and possible defects in equipment and processes so that maintenance can be scheduled before the equipment fails or performance deteriorates.
In-Depth Explanation
Predictive Maintenance relies on the condition monitoring of assets and systems to predict when maintenance will be required. Unlike preventive maintenance, which is based on time or usage intervals, predictive maintenance uses real-time data to determine the actual condition of the asset. This approach leverages various technologies such as IoT sensors, machine learning algorithms, and big data analytics to forecast when an asset is likely to fail or require maintenance.
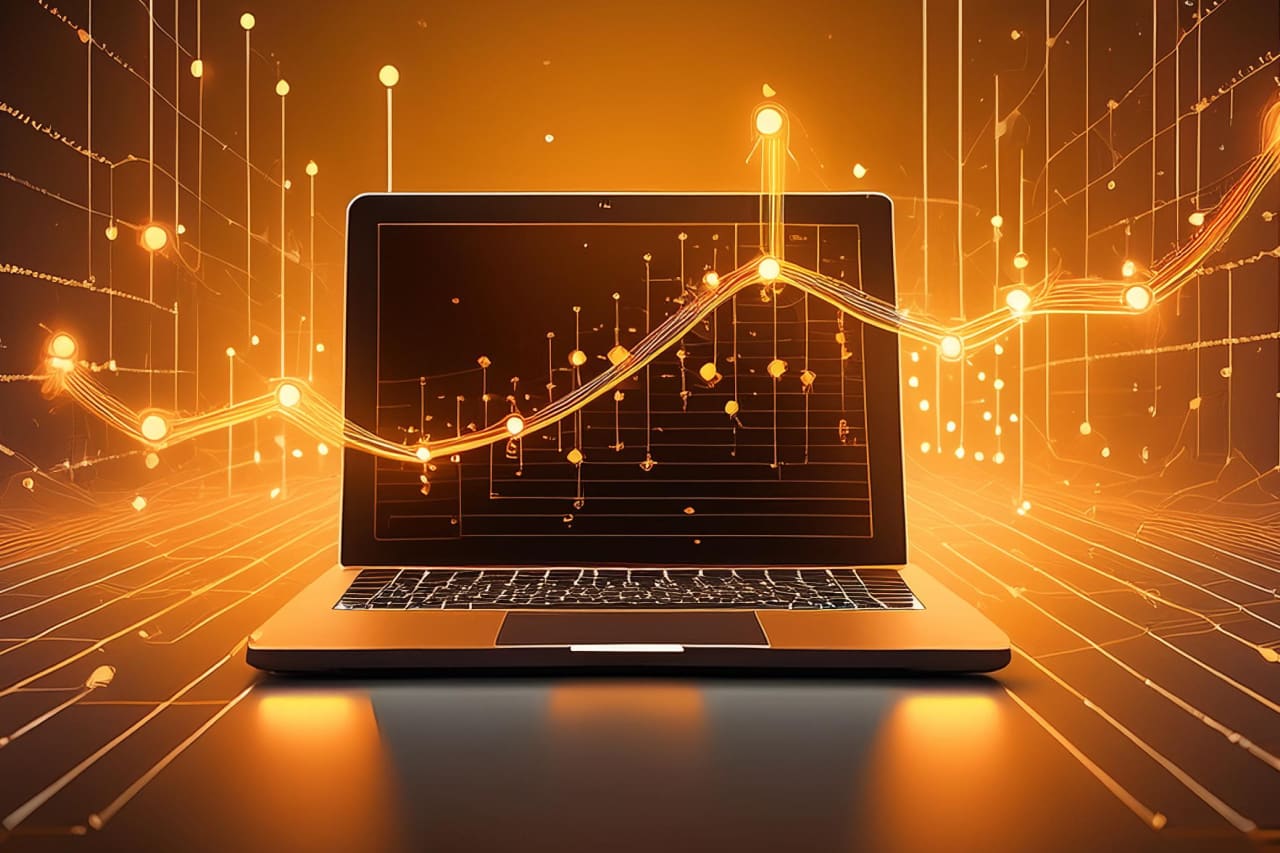
By analyzing patterns and trends in the collected data, predictive maintenance aims to identify the optimal time for maintenance activities, maximizing asset uptime while minimizing unnecessary maintenance. This approach is a key component of modern asset lifecycle management and plays a crucial role in optimizing the total cost of ownership (TCO) of assets.
Key Components of Predictive Maintenance:
- Condition Monitoring: Continuous tracking of asset performance and health.
- Data Collection: Gathering data from sensors, operational systems, and other sources.
- Data Analysis: Using advanced analytics to identify patterns and predict failures.
- Predictive Models: Algorithms that forecast when maintenance will be required.
- Integration with CMMS: Connection with Computerized Maintenance Management Systems for scheduling and execution.
Applications in Asset Management
Predictive Maintenance offers several benefits in asset management:
- Reduced Downtime: By predicting failures before they occur, downtime can be minimized.
- Cost Savings: Maintenance is performed only when necessary, reducing overall maintenance costs.
- Extended Asset Life: Timely interventions can prolong the useful life of assets.
- Improved Safety: Early detection of potential failures can prevent accidents.
- Optimized Resource Allocation: Maintenance resources can be allocated more efficiently based on actual needs.
- Enhanced Product Quality: Well-maintained equipment is more likely to produce high-quality output consistently.
Current Trends and Future Predictions
- AI and Machine Learning Advancements: More sophisticated algorithms for more accurate failure predictions.
- Integration with Digital Twins: Use of digital twin technology for advanced simulation and predictive modeling.
- Edge Computing for Real-time Analysis: Processing data closer to the source for faster decision-making.
- Augmented Reality in Maintenance Execution: Using AR to guide technicians during maintenance procedures.
- Predictive Maintenance as a Service: Cloud-based solutions making predictive maintenance more accessible to smaller businesses.
Best Practices for Implementing Predictive Maintenance
- Start with Critical Assets: Begin by focusing on the most critical or expensive assets.
- Ensure Data Quality: Implement robust data collection and validation processes.
- Combine Domain Expertise with Data Science: Integrate knowledge from maintenance experts with data analysis insights.
- Continuous Model Improvement: Regularly update and refine predictive models based on new data and outcomes.
- Change Management: Prepare the organization for the shift from reactive to predictive maintenance culture.
- Integrate with Existing Systems: Ensure predictive maintenance tools work seamlessly with other asset management systems.
- Train Staff: Educate maintenance teams on new technologies and processes.
Challenges and Considerations
- Initial Investment: Implementing predictive maintenance can require significant upfront costs in sensors and analytics tools.
- Data Interpretation: Accurately interpreting complex data and acting on predictions can be challenging.
- Integration with Existing Systems: Connecting predictive maintenance tools with existing maintenance and asset management systems.
- Skill Gap: May require new skills in data analysis and IoT technologies.
- False Positives/Negatives: Balancing the sensitivity of predictive models to avoid unnecessary maintenance or missed failures.
- Data Security: Protecting sensitive operational data collected for predictive maintenance.
Frequently Asked Questions
Q: How does predictive maintenance differ from preventive maintenance?
A: While preventive maintenanceis based on fixed schedules, predictive maintenance uses real-time data and analytics to determine when maintenance is actually needed.
Q: What types of data are used in predictive maintenance?
A: Common data types include vibration analysis, oil analysis, thermal imaging, acoustic data, and operational parameters like temperature, pressure, and power consumption.
Q: How accurate are predictive maintenance forecasts?
A: Accuracy can vary but generally improves over time as more data is collected and models are refined. Many systems can predict failures weeks or months in advance with high accuracy.
Q: Is predictive maintenance suitable for all types of assets?
A: While beneficial for many assets, predictive maintenance is most cost-effective for critical or expensive assets where failures would result in significant costs or downtime.
Q: How does predictive maintenance impact asset lifecycle management?
A: By optimizing maintenance timing, predictive maintenance can significantly extend asset life, reduce lifecycle costs, and improve overall asset performance and reliability.
Related Terms
- Condition-Based Maintenance: A maintenance strategy that is a precursor to predictive maintenance.
- Internet of Things (IoT): The network of connected devices that often provides data for predictive maintenance.
- Machine Learning in Asset Management: The use of AI algorithms to analyze data and make predictions.
- Reliability Centered Maintenance (RCM): A process to determine the most appropriate maintenance approach for assets.
- Total Cost of Ownership (TCO): Predictive maintenance can significantly impact the overall TCO of assets.
Conclusion
Predictive Maintenance represents a significant advancement in maintenance strategies, leveraging the power of data analytics and IoT to optimize asset performance and reliability. By enabling organizations to perform maintenance only when it's truly needed, predictive maintenance can lead to substantial cost savings, improved asset longevity, and enhanced operational efficiency.
As technology continues to evolve, predictive maintenance is becoming increasingly accessible and essential for organizations looking to stay competitive in asset-intensive industries. The integration of AI, machine learning, and advanced sensor technologies promises to make predictive maintenance even more accurate and valuable in the future. For organizations seeking to optimize their asset management practices, implementing a well-designed predictive maintenance program can be a game-changing strategy, driving improved performance, reduced costs, and enhanced competitiveness.
Other glossary terms
A - B - C
D - E - F
G - H - I
J - K - L
M - N - O
P - Q - R
V - W - X
Y - Z
Stop Losing Money on Missing Equipment
Join 1,000+ teams who've eliminated $2M+ in asset losses. Start saving money today - setup takes 30 minutes.