Inventory Management
Inventory Management is the systematic approach to sourcing, storing, and selling inventory—both raw materials (components) and finished goods (products). In the context of asset management, it encompasses the tracking and control of all assets an organization uses or maintains.
In-Depth Explanation
In asset management, inventory management goes beyond traditional retail or manufacturing contexts. It encompasses the tracking and control of all assets an organization uses or maintains, including IT equipment, tools, spare parts, and consumables. Effective inventory management ensures that the right assets are available in the right quantities at the right time, while minimizing carrying costs and reducing the risk of stockouts or overstock situations.
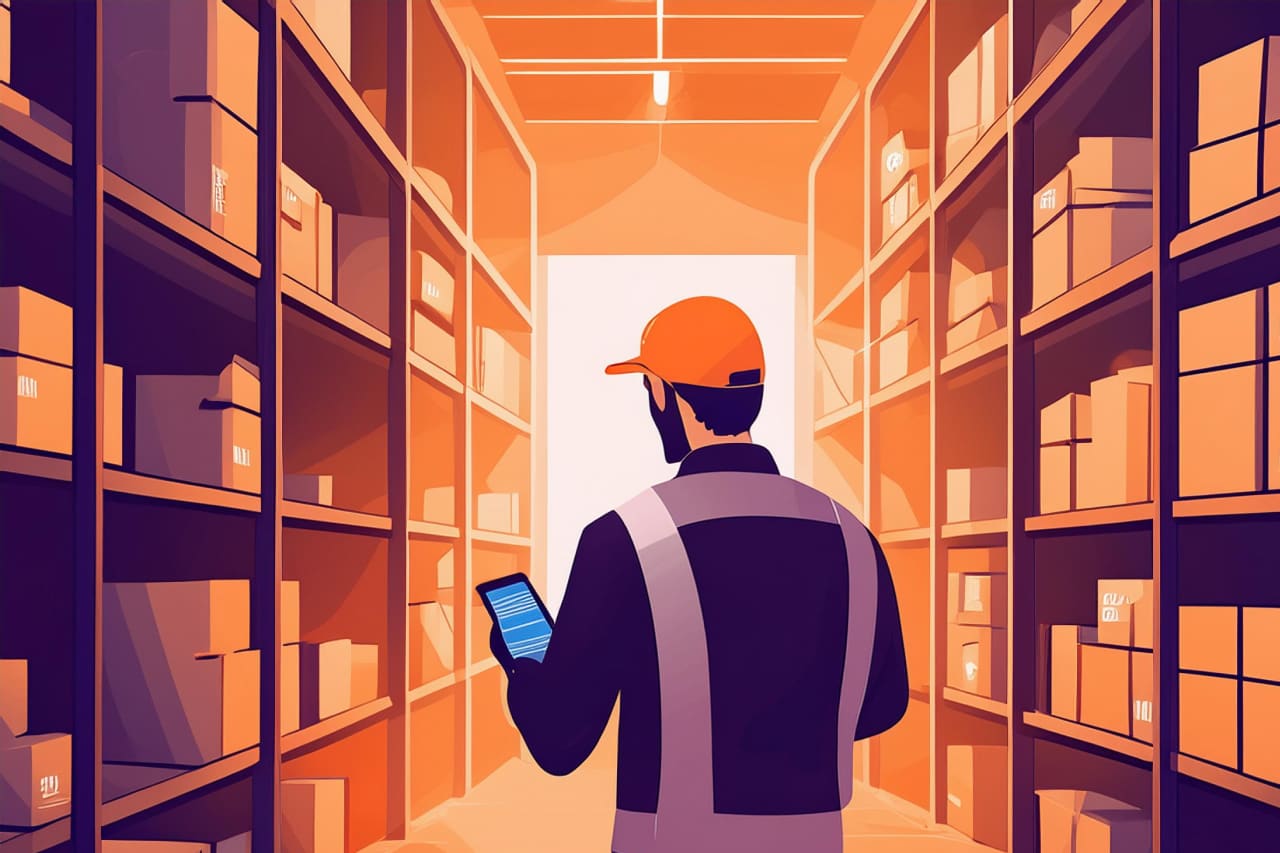
Inventory management is closely related to asset tracking but focuses more on quantities, usage rates, and replenishment processes rather than the location and status of individual items.
Key Components of Inventory Management:
- Demand Forecasting: Predicting future needs for inventory items.
- Stock Control: Maintaining optimal inventory levels.
- Asset Tracking: Monitoring the location and status of inventory items.
- Reorder Point Planning: Determining when to replenish inventory.
- Inventory Valuation: Assessing the financial value of inventory.
- Supplier Management: Managing relationships with suppliers for efficient replenishment.
Applications in Asset Management
Inventory Management offers several benefits in asset management:
- Cost Reduction: By optimizing inventory levels, organizations can reduce carrying costs and minimize waste.
- Improved Cash Flow: Efficient inventory management frees up capital that would otherwise be tied up in excess stock.
- Enhanced Productivity: Ensuring the right assets are available when needed improves operational efficiency.
- Better Decision Making: Accurate inventory data supports informed decisions about asset procurement and allocation.
- Risk Mitigation: Proper inventory management reduces the risks of stockouts, overstock, and obsolescence.
- Maintenance Support: Ensures availability of spare parts and consumables for preventive maintenance activities.
Current Trends and Future Predictions
- AI and Machine Learning in Demand Forecasting: Advanced algorithms are being used to improve the accuracy of demand predictions.
- IoT Integration: Internet of Things devices are enabling real-time tracking and automated inventory updates.
- Blockchain for Supply Chain Transparency: Blockchain technology is being explored to enhance traceability and security in inventory management.
- Robotic Process Automation (RPA): Automation of routine inventory management tasks is increasing efficiency and reducing errors.
- Sustainable Inventory Practices: Growing focus on environmentally friendly inventory management, including reducing waste and optimizing transportation.
Best Practices for Implementing Inventory Management
- Use Inventory Management Software: Leverage technology to automate tracking and reporting.
- Implement Barcoding or RFID: Use these technologies for accurate and efficient asset tracking.
- Regular Audits: Conduct periodic physical counts to ensure accuracy of inventory records.
- ABC Analysis: Categorize inventory items based on their value and usage frequency.
- Train Staff: Ensure all relevant personnel understand inventory management procedures.
- Optimize Reorder Points: Use data analytics to determine the most efficient reorder points and quantities.
- Implement Just-in-Time (JIT) Practices: Where appropriate, adopt JIT principles to reduce carrying costs.
Challenges and Considerations
- Balancing Act: Finding the right balance between having enough inventory and avoiding excess.
- Accuracy: Maintaining accurate inventory records can be challenging, especially for large or diverse inventories.
- Changing Demand: Adapting to fluctuations in demand for different inventory items.
- Obsolescence: Managing the risk of inventory becoming obsolete, especially for technology assets.
- Integration: Ensuring inventory management systems integrate well with other business systems.
- Global Supply Chain Complexities: Managing inventory across different locations and navigating global supply chain challenges.
Frequently Asked Questions
Q: What's the difference between perpetual and periodic inventory systems?
A: A perpetual inventory system continuously updates inventory records as transactions occur, while a periodic system updates inventory at set intervals through physical counts.
Q: How does inventory management affect a company's financial statements?
A: Inventory is an asset on the balance sheet. Effective inventory management impacts the balance sheet, income statement (through cost of goods sold), and cash flow statement.
Q: What is safety stock, and why is it important?
A: Safety stock is extra inventory kept on hand to prevent stockouts. It's important for managing uncertainties in supply and demand, ensuring business continuity.
Q: How can technology improve inventory management?
A: Technology like RFID, IoT sensors, and AI can improve inventory tracking accuracy, automate reordering processes, enhance demand forecasting, and provide real-time visibility into inventory levels.
Q: What is the Economic Order Quantity (EOQ), and how is it used?
A: EOQ is a calculation used to determine the optimal quantity of inventory to order to minimize total inventory costs. It balances ordering costs with holding costs.
Related Terms
- Asset Tracking: Closely related to inventory management, focusing on individual asset locations and status.
- Supply Chain Management: Broader discipline that includes inventory management as a key component.
- Just-In-Time (JIT) Inventory: An inventory strategy aimed at reducing carrying costs by receiving goods only as they are needed.
- Economic Order Quantity (EOQ): A calculation used to determine the optimal order quantity.
- Warehouse Management Systems (WMS): Software systems used to manage and control warehouse operations and inventory.
Conclusion
Inventory Management is a critical component of effective asset management, ensuring that organizations have the right assets available when and where they're needed. By optimizing inventory levels, organizations can reduce costs, improve operational efficiency, and make better-informed decisions about asset procurement and allocation.
As technology continues to evolve, inventory management practices are becoming increasingly sophisticated, offering new opportunities for optimization and efficiency in asset management. The integration of AI, IoT, and blockchain technologies is set to revolutionize inventory management, providing unprecedented levels of accuracy, transparency, and predictive capability. For modern organizations, mastering inventory management is key to maintaining competitiveness, ensuring business continuity, and maximizing the value of their assets.
Other glossary terms
A - B - C
D - E - F
G - H - I
J - K - L
M - N - O
P - Q - R
V - W - X
Y - Z
Achieve Crystal-Clear Asset Management
Join 1000+ teams already optimizing their asset utilization with Shelf. Start your free trial today.